Encapsulation Systems
Wrapping your frame
Encapsulation systems for timber frames are often referred to as a 'wrap' for the skeletal structure provided by our large section timber frames, and underpins the overall energy performance for the lifespan of the building.
Once the ‘wrap’ has been installed and the windows & doors fitted it forms what we call a ‘safe & secure weathertight shell, the outer membranes keep the vast majority of weather out and the doors can be locked with materials stored inside.
At this stage the majority of the work required to finish a build is within the weathertight shell, importantly this can be done concurrently with the external cladding.
This further speeds up the build and takes the pressure off in regards to completing the installation of the external wall & roofing materials.
Being wind and watertight can also be critical to financing a self-build project, and some mortgage lenders will release funds at this point to complete this section of the build project, before the next phase begins. These key stages are:
- Land (with the minimum of outline planning permission)
- Substructure
- Wallplate/eaves height (just before the roof trusses go on)
- Wind and watertight roof tiled
- First fix
- Second fix
- Certified completion
You can find out more about self-build mortgages from Homebuilding & Renovating and Build It.
Carpenter Oak does not manufacture encapsulation systems but we are partnered with carefully selected companies to be able to offer a choice of systems to deliver a wrap for your frame if required.
There are pros and cons to different types of systems and we can help you find the one which best suits your particular project.
We have extensive experience in integrating panels and timber frame design, leveraging the strengths of each to ensure a cohesive and efficient building. We champion low energy houses and aspire for the majority of our new build clients to be net exporters of energy.
With almost 40 years of experience in bespoke projects we can work with modest or the most complex project designs, and support self-builders to reach stage 4 of a self-build mortgage where needed.
Please get in touch with us to find out more about our frame wrapping service and discover the options available.
The two main panels - SIPs and timber frame panels
The two main systems for wrapping your frame are both types of panels which are pre-manufactured in a factory.
There are many benefits to using prefabricated panels:
- Assurance that the building will perform well structurally and thermally
- Speed and ease of installation
- Excellent thermal and airtightness
- Great thermal bridging performance (PSI values)
We use computer-aided design (CAD) to aid the frame design process, working in 3D models facilitating collaboration among the frame designer, architect, and SIP manufacturer for a precise fit. SIPs or Timber frame, their role in the project, and the choice of system or insulating material can be discussed during the concept stage. The exact specification can be adjusted as the design evolves.
When integrated with a large section frame, SIPs and timber frame panels eliminate the need for further support from other materials such as steel, as the oak frame, combined with the panels, can support floors and roof panels.
Using pre-manufactured oak frames and SIPs or timber frame panels, a structure can be made watertight in approximately a month, reducing labour costs and weather-related delays.
The fundamental difference between a SIPs or timber frame panel is whether or not insulation itself is structural or not.
If you would like to know more about SIPs or timber frame panels and how they integrate with large section structural timber frames, please get in touch with us.
Engineered timber panels
There are other types of panels available which can be used to build the walls around your structural frame skeleton such as Cross Laminated Timber (CLT).
CLT is made from layers of boards which are glued together at right angles to each other. This creates rigid, strong and stable timber.
CLT is not often used as insulation panels as the thermal conductivity of timber (Lambda value) although much lower than masonry or steel is not as low as a material intended to be used as insulation. They are also manufactured before they come to your site and available with different insulation choices to augment their thermal performance.
Some benefits to using CLT are that it can have less impact on the environment (when sustainably sourced timber is used) and can be a cleaner type of construction (as they require less wet trades).
Engineered timber - for your frame
Engineered timber is available as a material for your structural frame. We work with Laminated Veneer Lumber (LVL) and Glue laminated timber (Glulam) and these can be crafted in the same way as well-known solid section timbers (like oak and Douglas fir) to create traditional mortice and tenon jointed frames, or equally, using mechanical (steel) connections for a frame.
LVL
LVL is engineered from many thin veneers of wood, can take heavy loads, and can be used as structural beams or for walls and roofs.
Glulam
Glulam is a type of structural engineered wood constituted by layers of relatively small section sized lumber bonded together with durable, moisture-resistant structural adhesives so that all of the grain runs parallel to the longitudinal axis.
At Carpenter Oak we often produce structural frames using Glulams with traditional jointing techniques or mechanical connections (steel).
Contact us to find out more about encapsulation systems
Book an initial consultation
Get in touch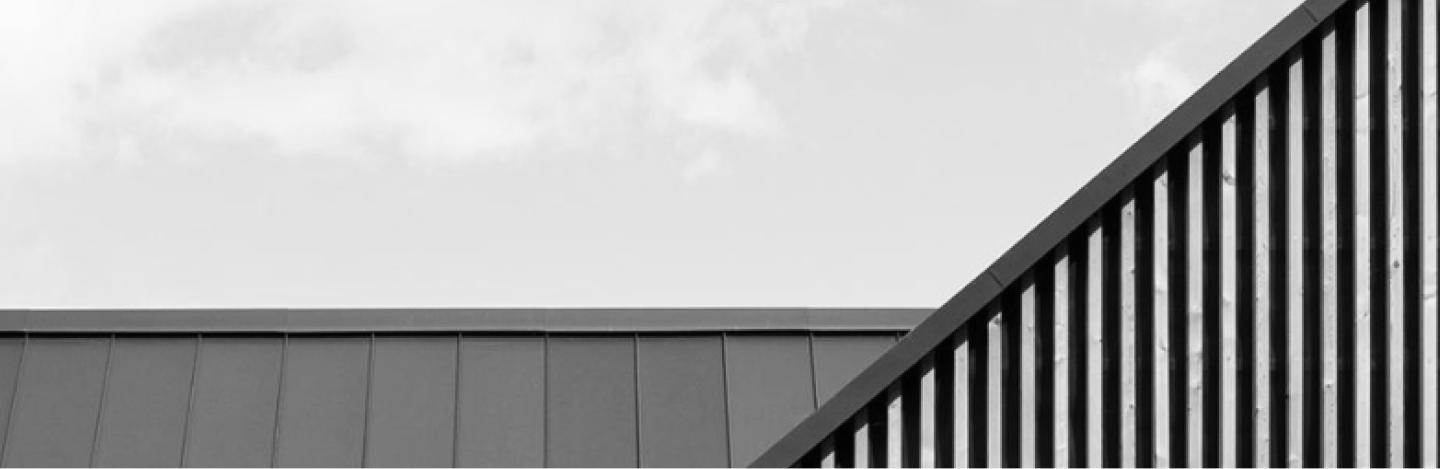